Degradation of building materials and evaporative flows: what are the links with waterproofing systems?
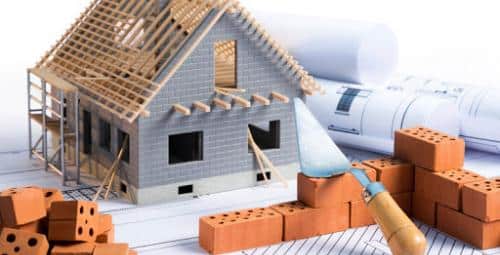
I believe that we all know the most common factors of degradation derived from external exposure conditions affecting the short and long term performance of the different materials used in civil or industrial construction, be they organic, synthetic or inorganic.
In any case, one of the most subtle concealed defects hidden under the laying substrates is the so-called “latent humidity inside the screeds”. This humidity remains cyclically active even in the presence of minimal amounts of water by weight. Therefore we must clearly distinguish the difference between free water and water chemically bound to the binding matrix, because even with minimal amounts of latent humidity, stored inside the screeds, there will always be an evaporative flow with an outflow path that starts from the inside of the screed towards the outside. These evaporative flows are even more marked both when the screed is damp and also when it is a particularly dry day. In any case, all absorbent materials (including good quality cement screeds) retain moisture and end up balancing with the ambient humidity: if there are very humid days, the screeds acquire more humidity by weight and if it is a dry day screeds end up losing moisture in weight. This behavior is well known as “equilibrium moisture with the environment”.
The characteristic formulation of screeds makes them extremely porous. Water is used to make them workable and allow the proper hardening. When the screeds are not given adequate time or conditions to dry, excess steam is generated and this phenomenon contributes to further movement of considerable masses of condensed water inside the screed.
It is therefore appropriate to provide for the installation of vapor barriers, as long as they are highly efficient. In the design phase we use special polyethylene sheets under the cement screed to protect a metallic aluminum foil of at least 50 microns placed in the middle, especially if lightened construction elements lie underneath this screed which retain even more large amounts of humidity.
Is it possible to control “hidden humidity” before laying the waterproofing layer?
An easy-to-use method consists in placing a 1 m2 high-thickness (200-350 micron) transparent polyethylene sheet, one for every 10 m2 of the substrate to be waterproofed. The perimeter of this sheet must be properly sealed with tape in strips with remarkable adhesive properties. Before completing the sealing, an electronic hygrometer (data logger) or analogue synthetic fiber hygrometer is placed under the polyethylene sheet. The evaporative flows are very slow dynamics, therefore it is necessary to wait at least 3 days before the correct reading; however, it is possible to check the humidity level indicated by the hygrometer day by day. With this methodology we are measuring the equilibrium humidity of the materials with the environment: in our case with a small environment confined to 1 m2 of surface created by us.
To transform the % value detected to an approximate quantity of water content by weight per square meter of screed, it is necessary to use parametric conversion scales for the different compositions of the different screeds.
By composition we mean not only the binding matrix of the screed, for example hydrated lime, hydraulic lime, eminently hydraulic lime, anhydrite, Portland cement of synthetic type (i.e. without high temperature fired clinker), but also the mix design of the screed (grain size and permeability of sands and various aggregates, also of the alveolar type).
Therefore, establishing an exact percentage of moisture content requires experience and comparative analyses. In any case, below, we propose one of the most used and reliable scales in the field of diagnostics of moisture content in weight referred both to measurements with capacitive hygrometers and to measurement with RH hygrometers in %.
In order to identify the most suitable areas in which to place the flow test, it is advisable to resort to the use of capacitive hygrometers. These instruments are now available cheaply and can measure the moisture content of a screed at variable depths up to 20-50 mm, providing very approximate values of the water content by weight of the screeds. Generally these instruments are supplied with different reference scales for different types of screeds, made with different hydraulic and aerial binders. The instrument display shows a dimensional scale generally from 0 to 100 or from 0 to 200 according to the electronic technology chosen for its construction. The number shown on the display must then be compared with the comparative scales supplied with the instrument’s user manual. Beware, all capacitive instruments are affected by errors in the presence of metals nearby, for example metal mesh under the screed and consequently if the metal mesh is placed in the instrument reading depth range, excessive values will be shown on the display. Before taking any measurement, it is therefore advisable to use a simple metal detector to exclude areas with reinforcing rods, nets or metal meshes under the cement surface.
These checks are of fundamental importance before applying any waterproofing coating and should not be considered an excessive operation since expert roofers perform these tests continuously.
Waterproofing systems and evaporative flows: management of any critical issues
The most common factors of degradation affecting waterproofing membranes are temperature, solar radiation, rain and ozone, the latter being given little consideration in the European culture of waterproofing. But there are also endogenous degradation factors that can create problems for the performance of waterproofing membranes.
One of the most frequent is the one called blistering.
Air bubbles in the membranes appear when air pockets (almost always humid air) are trapped between the membrane and the underlying support on which it is applied.
Even if we are dealing with screeds with low humidity, we must not forget that 1 cm3 of liquid water can transform into up to 1000 cm3 of vapor due to the heat generated by solar radiation.
This phenomenon obviously generates considerable pressures which act on the adhesion interface between the protective membrane and the support (i.e. screed) but also the acceleration of chemical reactions.
We must not forget that some polymers used in the construction industry (and in other applications) are very responsive to degradation due to alkaline hydrolysis, that is the reaction of hardened Portland cement (the true binding matrix of many hardened screeds) with water.
Although after 28 days of cement curing all of its fundamental crystallization reaction components reach maturity (the whole series of mono, bi and triplicates and alkaline aluminates), all these components remain reactive for many years. Therefore a high alkalinity also occurs when moisture flows through the cement screeds.
This alkalinity reaction can create interfacial degradation in the chain of many polymers: this is why Icobit invests time and economic resources in the research and development of suitable polymers and formulations.
In summary, the dynamics of the interfacial degradation of waterproofing membranes is very common in the presence of high humidity, high alkalinity and low-grade polymers.
As the sun warms the roof surfaces, those pockets of moist air expand and subject the membrane to elongation stress. If the membranes are not sufficiently tensile elastic, cracks and breaks may form due to the excessive pressure of the air vapor trapped under the sheath.
Even if the membrane does not crack, thanks to its significant level of tensile elongation (Icopas line for example), air bubbles still represent a problem destined to grow and can recur cyclically depending on the levels of humidity trapped under the sheath and lying even before the application of the sheath, solar heating cycles and their intensity also contribute directly to this phenomenon.
The evolution of the phenomenon is directly linked to:
- poor adhesion to the support (supports with non-stick treatments or not properly cleaned or not treated with special primers, especially if in the presence of humidity hidden deep inside or even under the screeds, tiles or supports in general);
- moisture content of the substrates before laying (lack of preventive measurement of the evaporative flows and the moisture content both on the surface and hidden in the deeper layers of the substrates);
- intensity of solar radiation;
- elastic capacity of the membrane. The more elastic and waterproof the membrane is, the more vapor coming from the substrate it will be able to trap.
How to control the alkaline attack under blistering phenomena after laying a waterproofing membrane
The most common diagnostic methodologies are as follows:
- Find the bubble
- Make a cross cut
- Open the flaps
- If the surface is sufficiently damp, insert litmus paper and compare the color with the reference scale
- If the surface is not sufficiently damp, proceed to wet it with a few drops of distilled water until it fails, wait 15-30 minutes and proceed to measure by immersing the litmus paper. If the water on the surface under the cut of the bubble has dried and does not wet the litmus paper, proceed to add a few drops of water and repeat the operation by placing again another litmus paper
- Once the work is completed, dry the support with absorbent paper in synthetic fiber (do not use cellulose). Restore the cut using a treatment with a quick-drying liquid membrane such as (Icoper Rapid, Icopas, Keep Line) by interposing a non-woven reinforcement between the two coats.
As soon as the paper soaks with liquid substance it produces a chemical reaction showing a color that can be compared with the numerical values of the color scale.
If the PH is alkaline it means that an interfacial degradation process is taking place. This could have been avoided firstly by measuring evaporative flows. In addition, the phenomenon could have been contained by using specific adhesion promoters with primer and/or barrier function (Icoblok by Icobit), and by installing special vents to get the trapped water out (Exit Air by Icobit).