Degrado dei materiali da costruzione e flussi evaporativi: quali legami con i sistemi impermeabilizzanti?
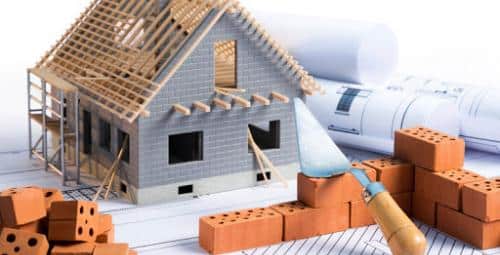
Credo che tutti noi conosciamo i fattori più comuni di degrado derivati dalle condizioni di esposizione esterne che interessano la prestazione a breve e lungo termine dei diversi materiali usati in edilizia civile o industriale, siano essi organici, sintetici ed inorganici.
In ogni caso uno dei vizi occulti più subdoli che si celano sotto i supporti di posa è la cosiddetta “umidità latente dentro i massetti”. Tale umidità rimane ciclicamente attiva anche in presenza di minime quantità di acqua in peso. Quindi dobbiamo distinguere bene la differenza tra acqua libera ed acqua chimicamente legata alla matrice legante, perché anche con minime quantità di umidità latente, immagazzinate dentro i massetti, si verificherà sempre un flusso evaporativo con un percorso di fuoriuscita che parte dall’interno del massetto verso l’esterno. Questi flussi evaporativi sono ancora più marcati sia quando il massetto è umido ma anche quando siamo in presenza di una giornata particolarmente asciutta. In ogni caso tutti i materiali assorbenti (inclusi i massetti cementizi di buona qualità) trattengono l’umidità e finiscono per equilibrarsi con l’umidità ambientale: se ci sono giornate molto umide i massetti acquistano più umidità in peso e se siamo in presenza di giornate asciutte i massetti finiscono per perdere umidità in peso. Questo comportamento è ben conosciuto come UEA (umidità di equilibrio con l’ambiente).
La formulazione caratteristica dei massetti li rende estremamente porosi. Si usa l’acqua per renderli lavorabili e consentire il corretto indurimento. Quando ai massetti non viene dato il tempo o le condizioni adeguate per asciugare si genera vapore in eccesso e questo fenomeno contribuisce ad ulteriori spostamenti di considerevoli masse di acqua condensata dentro il massetto.
È dunque opportuno prevedere l’installazione di barriere al vapore, a patto che siano ad alta efficienza. In fase progettuale utilizziamo sotto il massetto cementizio teli speciali di polietilene a protezione di una lamina di alluminio metallico di almeno 50 micron collocata nel mezzo, soprattutto se sotto questo massetto giacciono elementi costruttivi alleggeriti che ancor di più trattengono grandi quantità di umidità.
È possibile controllare “l’umidità occulta” prima della posa dello strato impermeabilizzante?
Un metodo di facile utilizzo consiste nel collocare un foglio di polietilene trasparente ad alto spessore (200-350 micron) di 1 m2, uno per ogni 10 m2 del supporto da impermeabilizzare. Il perimetro di questo foglio deve essere correttamente sigillato con nastro in strisce con spiccate proprietà adesive. Prima di ultimare la sigillatura si colloca sotto il foglio di polietilene un igrometro elettronico (data logger) o igrometro analogico a fibra sintetica. I flussi evaporativi sono dinamiche molto lente, dunque è necessario attendere almeno 3 giorni prima della corretta lettura; comunque è possibile verificare giorno per giorno il livello di umidità segnata dall’igrometro. Con questa metodologia stiamo misurando l’umidità di equilibrio dei materiali con l’ambiente: nel nostro caso con un piccolo ambiente confinato ad 1 m2 di superficie da noi creato.
Per trasformare il valore % rilevato ad un quantitativo approssimato di contenuto di acqua in peso per metro quadro di massetto è necessario utilizzare scale di conversioni parametriche alle differenti composizioni dei diversi massetti.
Come composizione non si intende soltanto la matrice legante del massetto ad esempio calce idrata, calce idraulica, calce eminentemente idraulica, anidrite, cemento portland di tipo sintetico (cioè senza clinker cotto ad alta temperatura), ma anche il mix design del massetto (granulometria e permeabilità di sabbie ed inerti vari anche di tipo alveolare).
Quindi la definizione di una percentuale esatta del contenuto di umidità richiede esperienza ed analisi comparative. In ogni caso, di seguito, proponiamo una delle scale più usate ed attendibili nel campo della diagnostica del contenuto di umidità in peso riferita sia alle misurazioni con igrometri capacitivi che alla misurazione con igrometri di URA in %.
Al fine di individuare le aree più idonee in cui posizionare il test dei flussi è consigliabile ricorrere all’utilizzo di igrometri capacitivi. Questi strumenti sono oggi reperibili a buon mercato e possono misurare il contenuto di umidità di un massetto a profondità variabili fino a 20-50 mm fornendo valori molto approssimati al contenuto di acqua in peso dei massetti. In genere questi strumenti vengono forniti con diverse scale di riferimento per diversi tipi di massetti, fatti con diversi leganti idraulici ed aerei. Nel display dello strumento si evidenzia una scala dimensionale generalmente da 0 a 100 oppure da 0 a 200 in funzione della tecnologia elettronica scelta per la sua costruzione. Il numero evidenziato nel display deve poi essere confrontato con le scale comparative fornite insieme al manuale di uso della strumentazione. Attenzione, tutti gli strumenti capacitivi risentono di errori in presenza di metalli nelle vicinanze, per esempio rete metalliche sotto il massetto e di conseguenza se la rete metallica è posizionata nel range di profondità di lettura dello strumento si evidenzieranno valori eccessivi nel display. Si consiglia dunque prima di eseguire qualsiasi misurazione di utilizzare un semplice cerca metalli per escludere le zone con ferri di armatura, reti o retine metalliche sotto la superficie cementizia.
Questi controlli sono di fondamentale importanza prima dell’applicazione di un qualsiasi rivestimento impermeabilizzante e non deve essere considerata un’operazione eccessiva dato che i roofers esperti eseguono di continuo questi test.
Sistemi impermeabilizzanti e flussi evaporativi: gestione delle eventuali criticità
I fattori più comuni di degrado che incidono sulle membrane impermeabilizzanti sono la temperatura, la radiazione solare, le piogge e l’ozono, quest’ultimo preso in poca considerazione nella cultura europea delle impermeabilizzazioni. Ma ci sono anche i fattori endogeni di degrado che possono creare criticità alle performance delle membrane impermeabilizzanti.
Una delle più frequenti è quella denominata blistering.
Le bolle di aria delle membrane si evidenziano quando si formano tasche di aria (quasi sempre aria umida) intrappolata tra la membrana e il sottostante supporto su cui essa viene applicata.
Anche se siamo in presenza di massetti con poca umidità non dobbiamo dimenticare che 1 cm3 di acqua allo stato liquido può arrivare a trasformarsi fino a 1000 cm3 di vapore grazie al calore generato dalla radiazione solare.
Questo fenomeno genera ovviamente pressioni considerevoli che agiscono nell’interfaccia di adesione tra la membrana protettiva ed il supporto (i.e. massetto) ma anche l’accelerazione di reazioni chimiche.
Non dobbiamo dimenticare che alcuni polimeri utilizzati dall’industria delle costruzioni (e in altre applicazioni) sono molto sensibili al degrado dovuto all’idrolisi alcalina, ovvero alla reazione del cemento portland indurito (la vera matrice legante di molti massetti induriti) con l’acqua.
Sebbene dopo 28 giorni di curing del cemento tutti i suoi componenti fondamentali di reazione di cristallizzazione arrivano a maturazione (tutta la serie di mono, bi e triplicati ed alluminati alcalini), tutti questi componenti rimangono reattivi per molti anni. Dunque una elevata alcalinità si verifica anche quando la umidità scorre attraverso i massetti cementizi.
Questa reazione di alcalinità può creare un degrado interfacciale nella catena di molti polimeri: questo è il motivo per cui Icobit utilizza tempo e risorse economiche nella ricerca e sviluppo di polimeri e formulati idonei.
In sintesi la dinamica del degrado interfacciale delle membrane impermeabilizzanti è molto comune se siamo in presenza di elevata umidità, elevata alcalinità e polimeri di bassa qualità.
Man mano che il sole riscalda le superfici dei tetti, quelle tasche d’aria umida si espandono e sottopongono la membrana a tensioni di allungamento. Se le membrane non sono sufficientemente elastiche a trazione possono formarsi fessure e rotture a causa della eccessiva pressione del vapore d’aria intrappolato sotto la guaina.
Anche se la membrana non fessura, grazie al suo significativo livello di allungamento a trazione (linea Icopas per esempio), le bolle d’aria rappresentano comunque un problema destinato a crescere e si può ripresentare ciclicamente in funzione dei livelli di umidità intrappolata sotto la guaina e giacente ancora prima dell’applicazione della guaina, anche i cicli di riscaldamento solare e la loro intensità contribuiscono direttamente a questo fenomeno.
La evoluzione del fenomeno è direttamente legata a:
- scarsa adesione al supporto (supporti con trattamenti antiaderenti o non correttamente puliti o non trattati con speciali primers, sopratutto se in presenza di umidità nascosta in profondità dentro o addirittura sotto i massetti, piastrelle o supporti in genere);
- contenuto di umidità dei supporti prima della posa (mancanza di misurazione preventiva dei flussi evaporativi e del contenuto di umidità sia superficiale che nascosta negli strati più profondi dei supporti);
- intensità della radiazione solare;
- capacità elastica della membrana. Più elastica ed impermeabile è la membrana e più vapore proveniente dal supporto riuscirà ad intrappolare.
Come controllare l’attacco alcalino sotto i fenomeni di blistering dopo la posa di una membrana impermeabilizzante
Le metodologie di diagnostica più comuni sono le seguenti:
- Individuare la bolla
- Praticare un taglio a croce
- Aprire i lembi
- Se la superficie è sufficientemente umida inserire la cartina di tornasole e comparare il colore con la scala di riferimento
- Se la superficie non è sufficientemente umida si procede a bagnarla con qualche goccia di acqua distillata fino a rifiuto, si attende 15-30 minuti e si procede a misurare immergendo la cartina di tornasole. Se l’acqua della superficie sotto il taglio della bolla si è asciugata e non bagna la cartina di tornasole procedere ad aggiungere qualche goccia di acqua e ripetere l’operazione appoggiando nuovamente un’altra cartina di tornasole
- Ultimato il lavoro asciugare il supporto con carta assorbente in fibra sintetica (non usare cellulosa). Ripristinare il taglio ricorrendo ad un trattamento con una membrana liquida a rapida asciugatura come per esempio (Icoper Rapid, Icopas, Linea Keep) interponendo fra le due mani un TNT di rinforzo.
Non appena la cartina si impregna di sostanza liquida produce una reazione chimica evidenziando un colore che è possibile comparare con i valori numerici della scala colorimetrica.
Se il PH sarà alcalino significa che è in atto un processo di degrado interfacciale. Lo si sarebbe potuto evitare innanzitutto misurando i flussi evaporativi. Oltre ciò, si sarebbe potuto contenere il fenomeno utilizzando specifici promotori di adesione con funzione di primer e/o barriera (Icoblok di Icobit), ed installando appostiti esalatori per far fuoriuscire l’acqua intrappolata (Exit Air di Icobit).