Détérioration des matériaux de construction et flux d’évaporation :quels liens avec les systèmes d’étanchéité?
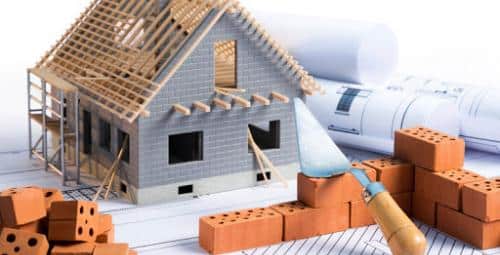
Je crois que tout le monde connaît les facteurs les plus communs de détérioration qui dérivent des conditions d’expositions extérieures qui intéressent la performance à court et long terme des matériaux utilisés dans la construction civile ou industrielle, qu’ils soient organiques, synthétiques et inorganiques.
En tout cas l’un des vices occults les plus sournois qui se cachent sous les supports d’installation et la soi disant « humidité latente à l’intérieur des chapes « . Cette humidité reste cycliquement active même en présence de petites quantités d’eau en poids. On doit donc bien distinguer la différence entre l’eau libre et l’eau chimiquement liée à la matrice liante, car même avec un minimum d’humidité latente, emmagasinée à l’intérieur des chapes, se vérifiera toujours un flux d’évaporation avec un parcours de fuite qui part de l’intérieur de la chape vers l’extérieur. Ces flux d’évaporation sont encore plus accentués soit quand la chape est humide mais aussi dans le cas d’une journée particulièrement sèche. Dans tous les cas tous les matériaux absorbants (inclus les chapes en ciment de bonne qualité) retiennent l’humidité et finissent par s’équilibrer avec l’humidité de l’environnement: s’il y a des journées très humides les chapes prennent plus d’humidité en poids et dans les journées sèches les chapes finissent par perdre de l’humidité en poids. Ce comportement est bien connu comme UEA (humidité d’équilibre avec l’environnement).
C’est leur formulation caractéristique qui rend les chapes extrêmement poreuses. On utilise de l’eau pour les rendre maniables et permettre un durcissement correct. Quand les chapes n’ont pas de temps ou des conditions adéquates pour sécher un excès de vapeur est généré et ce phénomène contribue à d’autres déplacements de masses considérables d’eau condensée à l’intérieur de la chape.
Il convient de prévoir l’installation de barrières à la vapeur à condition qu’elles soient de haute efficience. Dans la phase de planification on utilise sous la chape en ciment des toiles spéciales en polyéthylène pour protéger une feuille d’aluminium métallique de 50 micron au moins placée au milieu ,surtout si sous cette chape se trouvent des éléments de la construction allegés qui retiennent encore plus de grandes quantités d’humidité.
Est-il possible de contrôler « l’humidité occulte » avant la pose de la couche d’étanchéité?
Une méthode facile à utiliser est celle de placer une feuille de polyéthylène transparente épaisse (200-350 micron) de 1 m2, une pour chaque 10 m2 de support à imperméabiliser. Le périmètre de cette feuille doit correctement être scellé utilisant un ruban en bande très adhésif . Avant de terminer le scellage on place sous la feuille de polyéthylène un hygromètre électronique (enregistreurs de données) ou un hygromètre analogique fibre synthétique. Les flux d’évaporation sont des dynamiques très lentes, il est nécessaire d’atteindre au moins 3 jours avant d’avoir une lecture correcte ;de toute façon il est possible de vérifier jour après jour le taux d’humidité indiqué par l’hygromètre. Utilisant cette méthodologie on mesure l’humidité d’équilibre des matériaux avec la pièce : dans notre cas on a réalisé une petite pièce confinée à 1 m2 de superficie
Pour convertir la valeur % remarquée à une quantité approximative de contenu d’eau en poids pour mètre carré de chape il est nécessaire d’utiliser des échelles de conversion paramétriques aux differentes compositions des différentes chapes.
Quand on dit composition on n’entend pas seulement la matrice liante de la chape par exemple chaux hydratée , chaux hydraulique , chaux éminemment hydraulique,anydrite, ciment Portland synthétique (c’est -à dire cuit à haute température sans clinker), mais aussi le mix design de la chape ( granulométrie et perméabilité de sables et granulats divers également de type alvéolaire).
On peut dire que la définition d’un pourcentage exact du contenu d’humidité nécessite de l’expérience et d’ analyses comparatives. Dans tous les cas, ci-après. on propose l’une des échelles les plus utilisées et crédibles dans le domaine du diagnostic du contenu d’humidité en poids concernant les mesurages soit avec les hygromètres capacitifs que les hygromètres %HR.
Afin d’identifier les zones les plus appropriées où on peut positionner le test des flux il est conseillé d’utiliser les hygromètres capacitifs. Ces instruments sont disponibles à bon marché aujourd’hui et peuvent mesurer la teneur d’humidité d’une chape à des profondeurs variables jusqu’à 20-50mm fournissant des valeurs très approximatives de la teneur d’ eau en poids des chapes. Ces instruments sont généralement fournis avec différentes échelles de référence pour différents types de chapes réalisées avec différents liants hydrauliques et aériens . L’écran de l’instrument montre une échelle de dimension généralement de 0 à 100 ou bien de 0 à 200 en fonction de la technologie électronique choisie pour sa construction. Le nombre qui est sur l’écran doit ensuite être comparé aux échelles comparatives fournies avec le manuel d’utilisation de l’instrument. Attention, tous les instruments capacitifs sont affectés par les erreurs en présence de métaux dans les environs, par exemple les haies métalliques sous la chape et par conséquent si la haie métallique est positionnée dans la plage de profondeur de lecture de l’instrument , des valeurs excessifs seront montrées à l’écran. Avant d’effectuer n’importe quel mesurage on conseille d’utiliser un détecteur de métaux afin d’exclure les zones avec des tiges de renforcement , haies ou treillis métalliques sous la superficie en ciment.
Ces contrôles sont très importants avant d’appliquer n’importe quel revêtement imperméabilisant et on ne doit pas la considérer une opération exagérée vu que les couvreurs habiles font toujours ces types de contrôles.
Systèmes d’étanchéité et flux d’évaporation: gestion de tout problème critique.
Les facteurs les plus communs de détérioration qui ont une incidence sur les membranes imperméabilisantes sont la température , la radiation solaire, les pluies et l’ozone, ce dernier est peu considéré dans la culture européenne. Mais il y a aussi les facteurs endogènes de détérioration qui peuvent créer des problèmes aux performances des membranes imperméabilisantes.
L’un des problèmes les plus fréquents est celui appelé blistering en anglais.
Les bulles d’air des membranes apparaissent quand des poches d’air se forment( presque toujours de l’air humide) emprisonné entre la membrane et le support situé au dessous sur lequel elle est appliquée.
Même s’il s’agit de chapes qui ont peu d’humidité on ne doit pas oublier que 1 cm3 d’eau à l’état liquide peut arriver à se transformer jusqu’à 1000 cm3 de vapeur grâce à la chaleur produite par la radiation solaire.
Évidemment ce phénomène ne produit pas seulement des pressions considérables qui agissent dans l’interface d’adhésion entre la membrane de protection et le support ( c’est à dire la chape) mais aussi l’accélération de réactions chimiques.
On ne doit pas oublier que quelques polymères utilisés par l’industrie de la construction (et en d’autres applications) sont très sensibles à la dégradation due à l’hydrolyse alcaline, c’est-à dire à la réaction du ciment Portland durci (la véritable matrice liante de nombreuses chapes durcies)avec de l’eau.
Bien que après 28 jours de durcissement du ciment tous ses composants fondamentaux deréaction de cristallisation arrivent à maturation (toute la série de mono, bi et triplés et aluminates alcalins), tous ces composants restent réactifs pendant de nombreuses années. On vérifie aussi une alcalinité élevée lorsque l’humidité s’écoule à travers les chapes en ciment.
Cette réaction d’alcalinité peut créer une dégradation interfaciale dans la chaîne de beaucoup de polymères: c’est pour cela que Icobit emploie du temps et des resources économiques dans la recherche et le developpement de polymères et formulés appropriés.
En bref, la dynamique de la dégradation interfaciale des membranes imperméabilisantes est très commun en cas de taux d’humidité élevé , alcalinité élevée et polymères de mauvaise qualité.
Progressivement que le soleil rechauffe les superficies des toits ,ces poches d’air humide se répandent et soumettent la membrane à des tensions d’allongement. Si les membranes ne sont pas suffisamment élastiques à traction peuvent se former des fissures et ruptures à cause de l’excessive pression de la vapeur d’air emprisonnée sous la gaine.
Même si la membrane ne se fissure pas, grâce à son significatif niveau d’allongement à traction (ligne Icopas par exemple), les bulles d’air représentent toujours un problème destiné à se développer et qui peut se représenter de manière cyclique selon les niveaux d’humidité qui était déjà emprisonnée sous la gaine avant même de l’appliquer ,aussi les cycles de chauffage solaire et leur intensité contribuent directement à ce phénomène.
L’évolution du phénomène est directement liée à:
- Faible adhérence au support (supports avec des traitements antiadhérents ou pas nettoyés correctement ou pas traités avec des apprêts spéciaux surtout en présence d’humidité cachée en profondeur dans ou même sous les chapes, carreaux ou supports en général);
- taux d’humidité des supports avant la pose ( absence de mesure préventive des flux d’évaporation et du taux d’humidité à la fois en surface et caché dans les couches les plus profondes des supports);
- intensité de la radiation solaire
- capacité élastique de la membrane Si la membrane est plus élastique et imperméable elle arrivera à emprisonner plus de vapeur provenant du support
Comment contrôler l’attaque alcalin sous les phénomènes de blistering après la pose d’une membrane imperméabilisante
Les méthodologies de diagnose les plus communes sont les suivantes;
- Localiser la boule
- Faire une coupe en croix
- Ouvrir les bords
- Si la surface est suffisamment humide, insérez du papier de tournesol et comparez la couleur avec l’échelle de référence.
- Si la surface n’est pas suffisamment humide on la mouille avec quelques gouttes d’eau distillées jusqu’à il y en a assez, on attend 15-30 minutes et on mésure en plongeant le papier de tournesol. Si l’eau de la surface sous la coupe de la bulle est sèche et ne mouille pas le papier de turnesol on ajoute des gouttes d’eau et répéter l’opération à nouveau appuyant un autre papier de turnesol.
- Le travail terminé, essuyer le support avec du papier buvard en fibre synthétique (n’utilisez pas de cellulose). Rétablir la coupe utilisant une membrane liquide à séchage rapide comme par exemple( Icoper Rapid, Icopas, Linea Keep) interposant dans les mains un TNT de renfort.
Dès que le papier s’imbibe de la substance liquide il produit une réaction chimique montrant une couleur qu’on peut comparer aux valeurs numériques de l’échelle colorimétrique.
Si le PH est alcalin il signifie qu’il s’agit d’un procédé de dégradation interfaciale. Avant tout on l’aurait pu éviter mesurant les flux d’évaporation Outre cela on aurait pu contenir le phénomène utilisant des promoteurs d’adhésion spécifiques avec une fonction d’apprêt et /ou barrière (Icoblok de Icobit), et installant des ventouses spéciales pour faire évacuer l’eau emprisonnée (Exit Air di Icobit).